Summary:
How to Choose the Right Telescopic Curved Conveyor for Your Business
Understanding the Benefits of Telescopic Curved Conveyors
Key Factors to Consider When Choosing a Telescopic Curved Conveyor
Different Types of Telescopic Curved Conveyors
Installation and Maintenance of Telescopic Curved Conveyors
Understanding the Benefits of Telescopic Curved Conveyors
In today’s fast-paced logistics and manufacturing environments, efficiency and space utilization are crucial. Telescopic curved conveyors offer significant advantages in these areas due to their unique design.
Increased Efficiency in Material Handling
First and foremost, telescopic curved conveyors can greatly enhance material handling efficiency. Unlike traditional conveyors, these systems provide the flexibility needed to adapt to various workflows. When materials need to navigate complex paths, telescopic curved conveyors can effortlessly handle sharp turns and height variations, reducing wait times during transit. This acceleration not only speeds up overall production but also alleviates the burden on operators, allowing them to focus on more value-added tasks.
Space-Saving Design Features
Next, space utilization is a challenge many businesses face. The design of telescopic curved conveyors is specifically aimed at optimizing space, especially in confined work areas. Their retractable feature allows the equipment to be pulled back when not in use, freeing up valuable floor space. This is particularly important in warehouses and production lines, where companies can adjust the placement of the conveyors based on actual needs, ensuring that operational workflows run smoothly and efficiently.
Flexibility in Layout Configurations
Lastly, the flexibility of telescopic curved conveyors allows them to adapt to various layout configurations. Whether in a large manufacturing facility or a small warehouse, businesses can customize the path and angles of the conveyors according to their specific requirements. This adaptability not only enhances the flow of materials but also leaves room for future expansions and improvements. As demands change, companies can quickly adjust their conveyor setups to maintain optimal production line performance.
In summary, telescopic curved conveyors not only improve operational efficiency but also optimize space utilization and provide flexible layout solutions. Choosing this equipment can help businesses remain competitive in an ever-evolving market.
Key Factors to Consider When Choosing a Telescopic Curved Conveyor
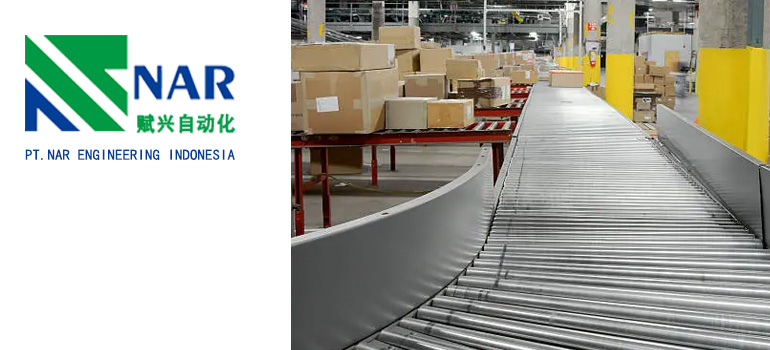
Selecting the right telescopic curved conveyor for your business requires careful consideration of several key factors. Each aspect can significantly impact your operational efficiency, safety, and overall productivity.
Load Capacity Requirements
One of the first factors to evaluate is the load capacity of the conveyor. Different applications may involve transporting varying weights and types of materials. It’s essential to determine the maximum load the conveyor will need to handle and choose a model that can accommodate this requirement. Overloading a conveyor not only affects its performance but can also lead to damage and safety hazards. Always consult manufacturer specifications to ensure the chosen conveyor meets your load demands.
Conveyor Length and Curve Radius
Next, consider the conveyor’s length and curve radius. The design of your workspace and the specific routing required for material flow will dictate these dimensions. A longer conveyor may be necessary for larger facilities, while the curve radius will determine how sharply the conveyor can turn. It’s crucial to assess your layout to ensure that the selected conveyor fits seamlessly into your operation, optimizing both space and efficiency.
Material and Durability Considerations
Another critical factor is the materials used in the conveyor’s construction. Depending on the type of products being transported, the conveyor may need to withstand various conditions, such as moisture, chemicals, or heavy impacts. For instance, if you are transporting fragile items, consider a conveyor with a gentler handling mechanism. Additionally, materials with high durability will extend the lifespan of the conveyor and reduce maintenance costs over time.
Flexibility and Customization Options
Flexibility is vital in today’s ever-changing business landscape. Look for telescopic curved conveyors that offer customization options, allowing you to adjust the conveyor’s design as your needs evolve. Features like adjustable heights, various curve configurations, and modular components can significantly enhance your operational flexibility. This adaptability ensures that your investment continues to deliver value as your business grows.
Safety Features and Compliance
Finally, safety should always be a top priority. Ensure that the telescopic curved conveyor you choose includes essential safety features, such as emergency stop buttons, guards, and proper shielding to prevent accidents. Additionally, verify that the conveyor complies with relevant safety standards and regulations. Investing in safety not only protects your workforce but also minimizes the risk of costly disruptions.
In conclusion, when choosing a telescopic curved conveyor, it’s essential to consider load capacity, length and curve radius, material durability, flexibility, and safety features. By evaluating these factors carefully, you can select a conveyor that meets your specific needs, enhancing your operational efficiency and productivity.
Different Types of Telescopic Curved Conveyors
When selecting a telescopic curved conveyor, it’s essential to understand the various types available, as each serves different purposes and applications. Here are some common types to consider:
Gravity-Fed vs. Powered Options
Gravity-fed telescopic curved conveyors rely on gravity to move materials. They are typically more cost-effective and require less maintenance, making them ideal for applications where the materials are lightweight and can flow naturally downhill. However, they may not be suitable for all situations, particularly where precise control over the speed and movement of items is required.
On the other hand, powered telescopic curved conveyors utilize motors to move materials. This option provides greater control over speed and allows for the handling of heavier loads. Powered conveyors are often equipped with advanced features like variable speed controls, which can be essential for optimizing efficiency in busy environments. Choosing between these options will depend on your specific operational needs and the type of materials you’re handling.
Adjustable vs. Fixed Designs
Telescopic curved conveyors come in both adjustable and fixed designs. Adjustable conveyors offer flexibility in terms of length and height, allowing operators to modify the setup based on the specific requirements of a task. This adaptability can be particularly beneficial in dynamic environments where workflows change frequently.
Conversely, fixed designs provide a permanent solution that may be more robust and require less frequent adjustments. These conveyors are often used in environments with consistent workflows where the material handling process does not vary significantly. The choice between adjustable and fixed designs will largely depend on your operational requirements and workspace constraints.
Industry-Specific Models
Different industries often have unique needs that require specialized conveyor systems. For example, in the food and beverage industry, conveyors must meet stringent hygiene standards. Stainless steel telescopic curved conveyors may be preferred for their ease of cleaning and resistance to corrosion.
In manufacturing settings, conveyors might be designed to handle heavy, bulky items. These heavy-duty telescopic curved conveyors typically feature reinforced structures and advanced drive systems to manage substantial loads efficiently.
Additionally, industries like pharmaceuticals or electronics may require conveyors with features designed for delicate items, ensuring minimal handling damage. It’s crucial to evaluate the specific requirements of your industry to select the most appropriate conveyor type.
In summary, understanding the different types of telescopic curved conveyors—including gravity-fed versus powered options, adjustable versus fixed designs, and industry-specific models—will help you make an informed decision. By aligning your choice with your operational needs, you can enhance efficiency and ensure that your material handling processes are optimized for success.
Installation and Maintenance of Telescopic Curved Conveyors
Proper installation and maintenance are crucial for ensuring the optimal performance and longevity of telescopic curved conveyors. Below are essential guidelines and best practices for both aspects.
Best Practices for Installation
Site Preparation Before installation, ensure that the site is properly prepared. This includes having a clean, level surface that can support the weight of the conveyor and any materials it will transport. Check for any obstructions, such as overhead beams or other equipment, that might interfere with the conveyor’s operation.
Following Manufacturer Guidelines Always refer to the manufacturer’s installation manual. These guidelines provide detailed steps for assembly, setup, and any electrical connections required. Adhering to these instructions helps prevent issues down the line and ensures safety compliance.
Alignment and Calibration Once the conveyor is in place, it’s essential to ensure that it is properly aligned. Misalignment can cause uneven wear and tear, leading to potential breakdowns. Check the angle of the curves and the height adjustments, calibrating as necessary to achieve a smooth and efficient operation.
Testing Before Full Operation After installation, conduct a thorough test of the conveyor system before fully deploying it. Run it empty to check for any unusual noises or vibrations. Gradually introduce materials to ensure the system operates smoothly under load, making any adjustments as needed.
Routine Maintenance Tips
Regular Inspections Implement a routine inspection schedule to identify any potential issues early on. Check for wear and tear on belts, rollers, and other components. Inspect electrical connections and safety features to ensure everything is functioning correctly.
Lubrication Keeping moving parts well-lubricated is essential for reducing friction and wear. Follow the manufacturer’s recommendations on lubrication intervals and types of lubricants to use. Regular lubrication can significantly extend the life of the conveyor.
Cleaning Procedures Maintaining a clean conveyor system is crucial for both hygiene and efficiency. Develop a regular cleaning schedule to remove dust, debris, and any materials that may have accumulated. For food and pharmaceutical applications, ensure that cleaning methods meet industry standards.
Addressing Minor Issues Promptly Don’t wait for minor issues to escalate into major problems. If you notice unusual noises, slowdowns, or other signs of trouble, investigate immediately. Addressing these issues promptly can prevent costly repairs and downtime.
Training Staff Ensure that all operators and maintenance staff are trained on the proper use and care of the telescopic curved conveyor. This includes understanding safety protocols, operation guidelines, and maintenance procedures. Well-trained staff can help minimize risks and enhance the efficiency of the conveyor system.
In summary, effective installation and maintenance of telescopic curved conveyors involve careful site preparation, adherence to manufacturer guidelines, routine inspections, and proper staff training. By following these best practices, you can ensure that your conveyor operates efficiently and reliably, ultimately contributing to the success of your operations.